Bajo este título, se celebró en Advanced Factories una conferencia en la que tres proveedores tecnológicos hablaron con el foco puesto en los procesos de estandarización, la integración de herramientas propias con ecosistemas abiertos, y en diferentes aproximaciones de cómo combinar esos niveles de herramientas, dependiendo del uso.
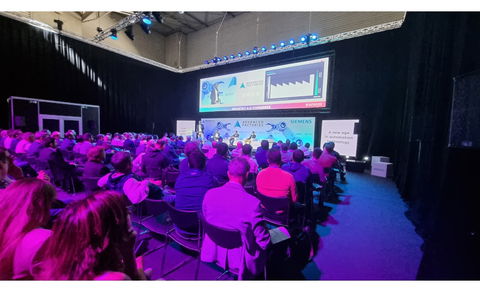
Desde de la perspectiva de estandarización de tecnologías a la hora de poder desplegar sistemas para la captura y el procesamiento de datos de IoT hacia cloud, y también centrado en un caso de uso para la gestión de la eficiencia energética, Sergio Muiña, gerente de ingeniería de ventas de automatización de Weidmüller, quiso poner el acento en un primer término en las comunicaciones de la infraestructura. “Si nos centramos en la capa superior de internet encontramos las comunicaciones inalámbricas con muchas tecnologías, ya que muchas veces una sola no es válida, sino que han de combinarse varias y escoger una u otra”. A este respecto, Muiña señaló que la elección depende de la solución que estemos buscando, de la velocidad y de la cantidad de datos que queramos transmitir, y de las distancias que tengamos que recorrer, entre otros aspectos. “Elegir una u otra va a depender de la aplicación y de lo que queramos resolver”, aduce Sergio Muiña, al tiempo que explica que “si nos vamos a capas que nos van a permitir mover la información con diferentes protocolos nos encontramos con los buses clásicos de los que podemos encontrar infinidad de ejemplos de campo, y de tecnologías que empiezan a surgir o que llevan años evolucionando y que empezamos a implementar los fabricantes en nuestras soluciones porque nos ayudan a estandarizar”.
El gerente de ingeniería de ventas de automatización de Weidmüller quiso puntualizar que, en esta capa, que es la parte en la que se produce la recogida de los datos, tiene lugar la digitalización de los mismos y un desplazamiento por las capas digital y física a través de una serie de aplicaciones abiertas, que van a ayudar a comunicar lo que cogemos en la parte de abajo para pasarlo a la parte superior. “De manera que desplazamos los datos de las capas físicas a las del cloud que están situadas en los diferentes puntos de las distintas fábricas. Lo que buscamos en muchas de estas tecnologías es que haya estándares comunes para podernos mover entre ellos”.
Proporcionar toda la cadena del dato para que la información recogida transfiera valor
Reflexionando acerca de si compensa llevar a cabo toda esta parte de la digitalización para realizar desarrollos teniendo en cuenta las posibilidades que brinda, Muiña responde afirmativamente, señalando que hay equipos que están pensados para estos procesos. “Muchos fabricantes, incluida la organización que represento, estamos pensando que todas estas tecnologías tienen que ser comunicables entre sí para hacernos entender entre diferentes interlocutores con diferentes soluciones, con la finalidad de que puedan integrarse dentro de nuestras plataformas, y para que las posibilidades que ofrece la solución sean integrables con los PLC”. Unos PLC que han de ser lo más estándar y abiertos posible, según el directivo, con la finalidad de que toda esa estandarización de las diferentes aplicaciones tenga cabida en su solución. Pasar por el proceso de digitalización para dar cabida a soluciones abiertas, según Muiña, va a ser posible a través de la conexión de los sistemas. “Se trata de conectar para saber lo que está ocurriendo dentro de nuestro sistema para a, continuación, digitalizar y, en tercer lugar, dar valor. Hemos de digitalizar lo que nos va a dar valor y, a partir de ahí, proporcionar toda la cadena del dato para que la información que estamos recogiendo nos de valor”.
Para Muiña, resulta difícil, en muchas ocasiones, saber lo que nos va a dar valor a priori, por lo cual muchas organizaciones tienden a recoger más datos de los que necesita. “La clave del éxito en esta fase de la digitalización consiste en poner sentido común a los datos que nos dan valor, y hacerlo a través de un análisis que suele discurrir de arriba abajo y no al revés”. Para este experto, ello no significa que todo lo que una firma de manufacturing tiene en la planta se haya de digitalizar y guardar, sino que ha de partir de una reflexión para saber qué es lo que proporciona valor. Por ello, Muiña insiste en que va a resultar necesario examinar las diferentes capas y dialogar con nuestros interlocutores para saber qué les da valor a la hora de adoptar las diferentes decisiones y, a partir de ahí, digitalizar las partes necesarias para abastecer a los equipos”, asegura Sergio Muiña.
Con respecto a los beneficios que aporta toda esa digitalización que implica el diálogo con diferentes interlocutores, a la vez que tener que comunicar en muchos casos diferentes buses de campo con diferentes tecnologías de comunicación, Sergio Muiña hace alusión a razones de globalidad y de eficiencia. “Estamos en un mercado global, y ello nos obliga cada día más a incrementar nuestra efectividad. En España todavía quedan muchas pequeñas y medianas empresas que siguen manteniendo lo que se conoce como ‘islas de información aisladas’, unas compañías que se están viendo forzadas a conocer lo que está pasando en esas islas y, para ello, el primer paso es atravesar un proceso de digitalización que va a conseguir ese incremento de la eficiencia que perseguimos. Ya que, si digitalizo y mido, sé lo que puedo mejorar, pero, si no mido nada, resulta complicado extraer esos valores para saber el grado de eficiencia que estoy consiguiendo y la velocidad de respuesta”.
Desde la perspectiva de Muiña, no es lo mismo esperar a los ‘rapports’ con datos procedentes de entornos no digitalizados que, seguidamente, se introducen en el ERP y posteriormente son estudiados, que disponer de esos valores en tiempo real y dar una respuesta inmediata. El aspecto de la coordinación es otro factor que gana peso con la digitalización, según Muiña, ya que, al disponer de diferentes sistemas y puntos que se han de comunicar entre sí, hay que proporcionar una respuesta a la cadena en cada uno de los pasos. Y añade: “si ha habido un proceso de digitalización, y tengo la certeza de lo que está pasando en cada uno de estos pasos, la coordinación será una tarea mucho más sencilla”.
Por lo que respecta a los retos de la digitalización, Sergio Muiña habla de la privacidad de unos datos que, en muchas ocasiones, están circulando en local, mientras que en otras se elevan esos datos al cloud para alcanzar la interoperabilidad entre plantas. “La privacidad es un reto que tenemos que mejorar, declara este experto, mientras hace mención a la ciberseguridad como otro gran desafío de la digitalización, “con la finalidad de que esos datos que se están moviendo sean seguros, y para que sean utilizados solamente por parte de la organización y que nadie no autorizado pueda llegar a ellos para alterarlos o compartirlos”. Para concluir, el gerente de ingeniería de ventas de automatización de Weidmüller expuso un caso de éxito de una compañía de tamaño mediano con un proyecto que pretendía reducir el consumo energético y cumplir con la ISA 50.001, al estar obligada por el tamaño y número de trabajadores de la empresa. “La solución fue definida a través de diferentes tecnologías, mientras que el cliente exportó parte de los datos que tenía en su scada a Azure porque lo quería integrar con su Power BI”. El valor aquí, según declara este entendido, fue “poder integrar todo lo que teníamos del cliente para darle una solución que permitiera ofrecer informes de estado en tiempo real, así como la gestión de alarmas, las visualizaciones de los datos tanto en los ordenadores como en planta, y el tener conocimientos, no solo de la planta en local donde está ubicado el scada, sino también de las distintas plantas que están localizadas en otros puntos de la geografía. A partir de aquí, el cliente puede integrar más KPI de producción”.
El edge fundamentado en almacenar, procesar y analizar los datos puede llevar años
Centrándose en las soluciones PLC Next, desarrolladas por la organización que representa, como pasarela hacia una visión de plataforma abierta que integra soluciones de terceros para la integración de tecnologías, Ramón Quirós, jefe de producto IMA de Phoenix Contact, sostuvo que cuando se empezó a hablar de industria 4.0 y del IoT cayeron en la cuenta de que el proceso de ‘Ioteneización’ no se iba a conseguir en un año ni en dos, sino que llevaría un tiempo mucho más largo en la mayoría de empresas, tuvieran el tamaño que tuvieran. “Hemos pasado de una posición de obtener el ‘feedback’ de lo que nuestros clientes esperarían de un ‘gateway’ IoT, y de un sistema de control, a aunarlo todo y ofrecerlo a nivel de campo”, señala Quirós.
Desde la perspectiva de la comercialización de equipo industrial, que es la actividad habitual de la firma, Ramón Quirós precisa que estas máquinas también serían suministradas para soportar procesos de IoT con la finalidad de poder cumplir con esas expectativas de los clientes. Los requisitos típicos que solicitan los clientes al sistema IoT a instalar –según este experto—pasan por una capacidad de utilizar los estándares de la industria como OPC UA o MQTT pero, sobre todo también, para que sean adaptables a lo que venga en el futuro. “Cada vez nos encontramos con mayor frecuencia a gente que programa, no ya con bloques de funciones o diagramas de contactos o texto estructurado, sino que lo hace directamente con lenguajes de alto nivel y también con modelos matemáticos y, sobre todo, está acostumbrado a integrar aplicaciones de código abierto para aprender a construir herramientas a través de un tutorial sin depender de la formación, marcas o de terceros”. Además, Quirós señala que los desarrolladores de tecnologías para usos de IoT tienden a hacer una arquitectura cada vez más abierta, que no esté sujeta a licencias, que tenga conectividad a la nube y, con la tendencia de esa mayor conectividad, que la ciberseguridad sea integrada de forma nativa e implementada en el desarrollo.
“Dentro de lo que es el estándar IoT, podríamos hablar de ‘cloud computing’ pero, como somos fabricantes de equipamiento industrial de hardware, vamos a referirnos al ‘edge computing’, donde el procesamiento de los datos se realiza en el borde de la red que define el entorno de las operaciones que llamamos OT a la infraestructura de tecnología de la información IT”. Para Quirós, una aplicación edge podría consistir en recopilar esos datos procedentes de las líneas de producción sin interrumpirlas y de una forma mínimamente invasiva, y decidir si esos datos son enviados a la nube con la finalidad de realizar un análisis con IA o sin ella o, inclusive; o bien si es preferible hacerlo en local, por una preocupación relacionada con la integridad de esos datos que la organización no desea compartir con terceros como Microsoft o Amazon.
“El equipo edge, tal y como lo concebimos en Phoenix Contact, tiene que ser un sistema que -si tiene la conectividad a internet a través de diferentes interfaces posibles, así como wifi o 5G- ha de disponer de la ciberseguridad implementada porque el equipo va a ser una puerta hacia la nube, o hacia un servidor de datos desde la parte de producción hacia la red IT. De manera que, todo lo que podamos leer a nivel de campo con esos dispositivos edge, vamos a ir viendo si los almacenamos, si los llevamos al ‘machine learning’ (ML) desde una base de datos local, si los llevamos a un tipo de scada u otro; o si, directamente, los subimos a una infraestructura de nube”. “El procesamiento de edge fundamentado en la técnica de almacenar para luego procesar y analizar esos datos no se hace en un día”, afirma Quirós, “sino que representa un paso a paso que, en función de las empresas, se va desarrollando a lo largo de meses y años, y también con algunas especificaciones internas”.
“Partiendo de un hardware existente, el concepto funcional de edge se lleva a cabo desde una máquina en formato PC con la capacidad de almacenamiento interno, también enfocando subredes entre sí; y derivando con los PLC de campo donde se sitúan tarjetas de entradas/salidas. De esta manera, el edge que proponemos en Phoenix Contact ya no consiste solamente en un gateway IoT que pueda leer equipos a nivel de campo, almacenarlos, pre-procesarlos y llevarlos a una base de datos local; la idea es saber qué expectativas tienen nuestros clientes hacia este mundo IoT y ofrecerles una tecnología de control también abierta. Un dos en uno”. De esta manera, este experto señala que hace cinco años desarrollaron la tecnología PLC Next en paralelo a su línea de PLC convencionales, “lo que significa que puedo programar el sistema de control en cualquiera de los lenguajes de alto nivel de forma nativa y compartiendo variables de manera consistente y totalmente abierta. Además, estos equipos disponen de un sistema operativo Linux donde el usuario tiene la posibilidad de instalar, mediante tecnología de contenedores, distintas aplicaciones de software de código libre para machine learning o herramientas IoT.
Otro aspecto importante, según Quirós pasa por disponer de certificados de componente edge “si se va a conectar con nubes de los proveedores de cloud pública como Google, Microsoft o AWS, o bien a clouds pertenecientes a otros proveedores. “Toda nuestra gama de tecnología PLCnext, que consta también de controladores PLC, han sido, desde su inicio en 2017, OPC UA server, un estándar que vamos a manejar en el futuro en la parte de OT para comunicar hacia arriba con sistemas scada, o hacia otros subsistemas entre sí”. Otro aspecto importante a tener en cuenta, según este experto, consiste en que el desarrollo de estos equipos ya se hizo teniendo en cuenta el estándar de ciberseguridad en entornos industriales, que es ISA 62443. “A día de hoy -señala- tiene el certificado de desarrollo de producto seguro 4.1 y, en un par de meses, tendremos la certificación 4.2; un estándar que permite reducir el riesgo de ciberseguridad en entornos de fabricación”. El sistema dispone de una herramienta para la visualización de páginas web donde se puede hacer un pequeño scada, y contamos con un marketplace digital en el que ofrecemos aplicaciones al igual que otras firmas, en donde se pueden encontrar librerías, conectores o ‘runtimes’ para actuar con bases de datos SQL, gestionar otros protocolos diferentes, manejar aplicaciones de terceros, hacer una conectividad VPN saliente hacia una nube de ‘telemanenimiento’ , o directamente APP -ya que se trata de código predesarrollado para ser cargado- y perder el mínimo tiempo en lo que podría ser la automatización de un bombeo o un control de palas en una turbina eólica, por ejemplo. Si, además, el usuario quiere instalar aplicaciones ‘dockerizadas’, la organización de Quirós utiliza directamente la herramienta de Docker. “Asimismo, podemos realizar diferentes visualizaciones y ‘dashboards’ y, a través del editor de páginas web que incorporamos, podemos obtener un scada web más o menos detallado porque, en definitiva, perseguimos la idea de adaptabilidad ilimitada”.
Portfolio, ecosistema y marketplace
Para saber de qué modo plantea la compañía que representa las soluciones de industrial edge combinándolas con un ecosistema de aplicaciones de terceros y marketplace, Alvaro Esteve, jefe de la unidad de negocio y automatización de fábricas de Siemens Digital Industries, agradeció a sus compañeros de speech que hubieran transitado por los estándares tecnológicos de IoT, como en el caso de Sergio Muiña; y de Ramón Quirós en el tema del edge. “Lo complicado en el universo de IoT, afirma Esteve, es el establecimiento de un estándar como ecosistema. Este es el punto clave y, desde Siemens Digital Industries estamos convencidos de ello; pero la realidad no nos acompaña”. Y es que este responsable señala que el 86% de las empresas, cuando se produce un hecho crítico, y debido también a la complejidad de los sistemas existentes en su propia fábrica, no está utilizando el IoT, sino que emplea la tecnología de internet de las cosas para los casos fáciles; por consiguiente, poco beneficio hay ahí. “Asimismo, el 45% de las empresas no sabe por dónde empezar a implantarlo, mientras que un 40% tiene dificultades a la hora de encontrar empresas o partners con la capacidad y experiencia suficiente para acometer esos proyectos. Esteve señala que estos datos han sido extraídos de Forbes y de la Harvard Business Analytics, al tiempo que puntualiza que: “resulta muy fácil desarrollar una aplicación nueva, pero tenemos que tener en cuenta que ha de convivir con otros sistemas, y tomar en consideración también el ciclo de vida de instalaciones que, en muchas ocasiones, llevan decenas de años funcionando sin problemas”. De manera que las nuevas aplicaciones orientadas a IoT han de ser flexibles, ya que tenemos que poder empezar por alguna parte de ese ciclo de vida, crear beneficio donde se requiera, a la vez que hemos de ser abiertos como ecosistema, lo que significa que ningún fabricante tiene toda solución”. En el caso de Siemens, el directivo señala que la firma dispone de toda la solución, “pero no es la mejor compañía en todos los campos; por consiguiente, tenemos seguir abiertos a tecnologías de otros fabricantes”.
“Para hacer alusión a lo que es IoT, tenemos que hablar de tres aspectos: el portfolio en donde se incluyen los apartados descritos por mis compañeros en ese campo del IoT; también tenemos que señalar al ecosistema y ver cómo juegan otros actores en ese terreno del internet de las cosas; y tenemos que tener en cuenta al marketplace, porque necesitamos agilidad y, si hay terceros actores, no pasamos por una tienda con un solo proveedor, sino que tenemos que acudir a un marketplace, del tipo Amazon, desde donde yo adquiero mis soluciones y monto mis arquitecturas de software para IoT”.
En el apartado correspondiente al portfolio, este experto define el industrial edge como la integración IT/OT desde el OT, donde ha de primar la robustez, la fiabilidad y la facilidad de despliegue y de uso. “Es decir, estamos hablando de que no tengamos que tener informáticos expertos en código abierto, ni bibliotecas especializadas para montar nuestra aplicación IoT. Tiene que ser nuestro personal de automatización o nuestro personal incluso eléctrico de la parte industrial quien haga estos despliegues”. Por lo que respecta a la capa edge, Alvaro Esteve quiere aclarar que no actúa como sustituto al cloud. ”Desde el edge, tenemos los equipos críticos para que la instalación funcione, nuestros procesos sean fiables 24x7, y la nube. No obstante, disponemos de una capa intermedia en la propia fábrica que nos permite resolver ciertos problemas relacionados con la latencia por tener las aplicaciones en nube, problemas de seguridad de nube –cuando el know-how y el propio proceso se lleva a cloud--, en tiempo real y, si puede, ya no solo obtenemos buenos consejos a través de KPI, sino que buscamos cerrar el círculo optimizando los parámetros de los PLC”, señala.
En el apartado correspondiente a la instalación de aplicaciones de internet de las cosas en una arquitectura IoT que ya esté funcionando, el directivo insiste en la inclusión de máquinas, líneas de producción con sus PLC de diferentes fabricantes, HMI, un scada que centralice el control de la línea completa o de la planta donde se conectan los equipos edge que van a integrar los datos de diferentes fabricantes que tienen distintas conexiones, y tener en cuenta otros aspectos con la finalidad de captar todos esos datos y procesar aquello que no puede hacer con la instalación existente. “Ese procesamiento relativo al valor del dato lo voy a hacer con esos equipos que, a su vez, van a intercambiar datos con el scada. De manera que habrá datos que al scada le interesen porque los he procesado con el edge; mientras que cierta información procedente del edge habrá sido extraída del scada”. Para este experto, esto requiere un despliegue con un gestor, lo que plantea diferencias en el sistema industrial edge a la hora de tener la capacidad de hacer una infraestructura totalmente flexible sabiendo, en todo momento, qué aplicaciones corren en qué equipo e, incluso, programar las actualizaciones en horarios en los que la planta está parada o la producción es mínima”. Esteve quiere dejar claro que los gestores de la planta de fabricación IoT podrían tener interés en disponer de una conexión a la nube para acceder a ML con la finalidad de entrenar ‘machine learning’ en cloud, para luego desplegar el algoritmo ya entrenado en la aplicación edge, “y, aquí, entraría en la nube de Siemens, o en cualquier otra de las nubes que haya en el mercado, y dotado de desarrollo de aplicaciones con código ‘low code’. Asimismo, el edge mangement podría estar ‘on premise’, o bien en la nube”.
Fuente: www.infoplc.net